Adapting to Change: The Shift in Global Supply Chains and How Flexible Robotics Are Leading the Way
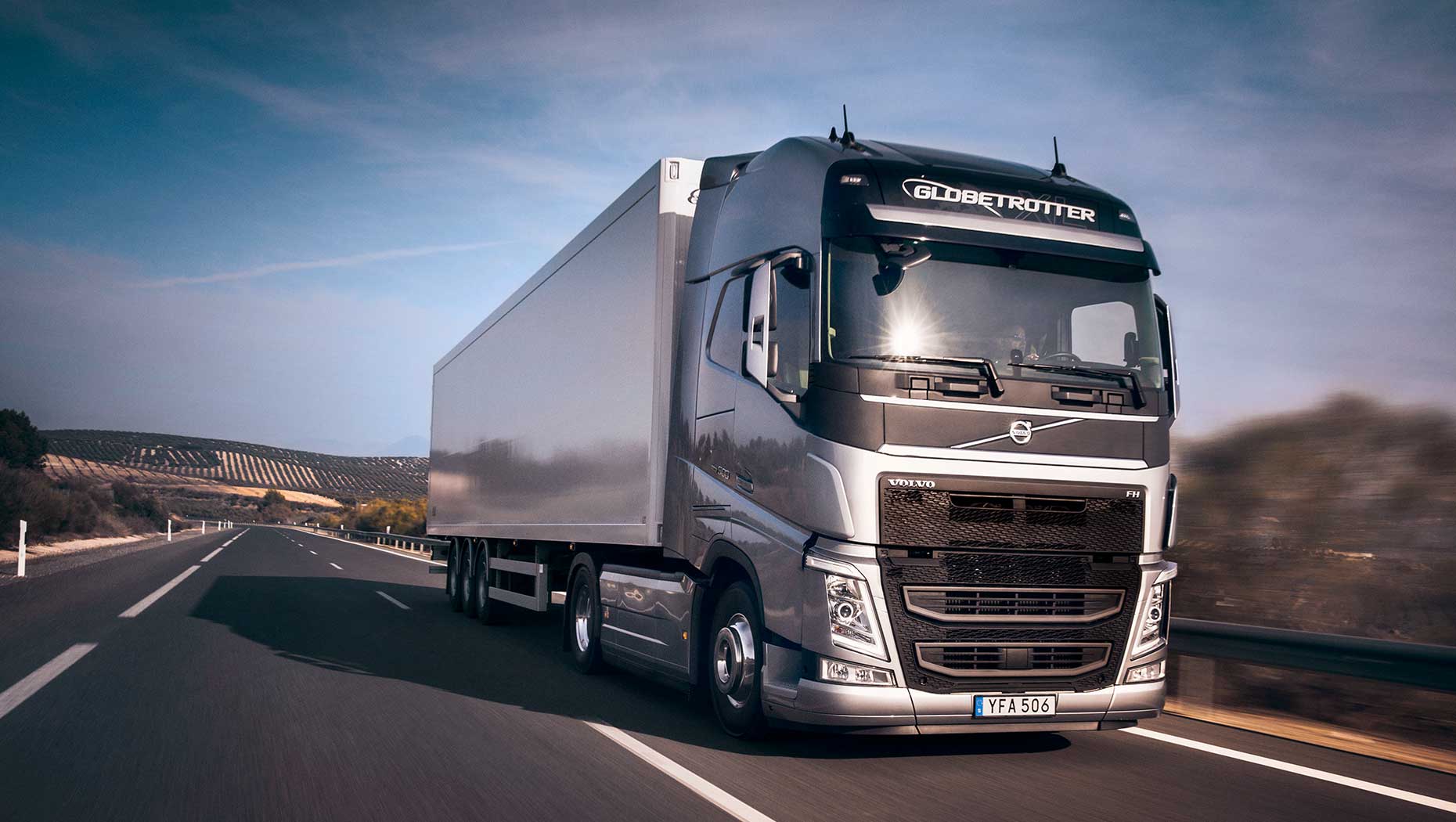
Introduction:
The global supply chain landscape has undergone dramatic shifts over the past five years, with disruptions caused by the pandemic highlighting the fragility of long-distance sourcing. As companies seek to adapt to rapidly changing market conditions, many are shifting production closer to home. This blog post explores how the pandemic has reshaped supply chain strategies, how European manufacturers are adjusting to this change, and how OpiFlex's innovative robotics solutions are helping companies future-proof their factories with greater flexibility and speed.
The Shift Towards Regional Supply Chains
The pandemic has undeniably exposed the vulnerabilities of global supply chains, particularly those heavily reliant on suppliers from distant regions such as Asia. Jacob Wallenberg, Chairman of Investor, notes that for many years, companies leaned heavily on these far-reaching networks, but this dependency proved problematic when factories shut down and transportation networks faltered. In response to this disruption, more companies are now focusing on suppliers closer to home, particularly in Europe and its neighboring regions. This shift isn't just about geographic proximity—it’s about building more resilient and agile supply chains.
Wallenberg underscores this change: "Historically, we took a lot of our components from Asia and other distant parts of the world. Now, the focus is much more on our nearshore regions, where we can have better oversight and avoid future disruptions." This regionalization of supply chains is not only a response to the pandemic but also a long-term strategy to reduce risk and maintain control over critical production elements. The idea of relying on multiple supply chains—rather than just one—is gaining traction among businesses aiming for increased resilience.
Nearshoring: A Strategic Move for Flexibility
In response to these challenges, many manufacturers are shifting production closer to their target markets, with countries like Turkey and Morocco emerging as key hubs for production. Major companies, including Volvo, have already been bringing their suppliers closer to their European operations even before the pandemic, but the crisis has accelerated this trend. Martin Lundstedt, CEO of Volvo, explains that the company had already established a regionalized supplier network, but with the pandemic’s impact, this strategy has become even more crucial.
The benefits of nearshoring are clear: reduced lead times, lower transportation costs, and the ability to quickly adjust production volumes. For industries that require frequent product changes and the ability to pivot quickly in response to market demands, this shift is a game-changer. The need for flexibility in manufacturing has never been greater, and European factories are increasingly well-positioned to offer the responsiveness that companies require.
The Need for Flexible Production Lines
While geographic proximity is important, the real challenge lies in the ability to adapt production lines quickly. In today’s fast-paced manufacturing environment, companies must be able to respond to fluctuating demand, shift between different product types, and adjust volumes with minimal downtime. This is where OpiFlex’s advanced robotics and automation solutions come in.
OpiFlex offers flexible, mobile robots that can be integrated into production lines with ease, providing manufacturers with the ability to reconfigure their workflows in a matter of minutes. The patented Dynamic Program Generator allows for rapid programming of new products, cutting integration time to just 1-5 minutes, which is 50 times faster than traditional programming methods. This ability to quickly adapt production lines to changing needs is key to maintaining a competitive edge in an increasingly volatile market.
How OpiFlex Meets the Demand for Future-Proof Factories
The future of manufacturing lies in the ability to create agile, responsive production environments. OpiFlex’s robotics solutions provide the flexibility needed to build future-proof factories capable of handling rapidly changing demands. With the ability to deploy multiple robots in sequence, each handling products within a 1-second cycle time, OpiFlex allows manufacturers to optimize production efficiency while maintaining the highest safety standards.
Additionally, OpiFlex's patented fenceless safety solution means that robots can work alongside operators without the need for costly barriers or restrictive safety protocols. This unique feature not only reduces the need for additional infrastructure but also optimizes the use of space on the factory floor, enhancing overall productivity.
Conclusion:
The pandemic has catalyzed a shift towards more localized and flexible supply chains, with companies increasingly recognizing the importance of agility in manufacturing. By bringing production closer to home and adopting flexible automation solutions like OpiFlex, businesses are better positioned to respond to future challenges. OpiFlex’s innovative robotic systems are helping manufacturers future-proof their factories, enabling them to remain competitive in a rapidly changing world.
Call to Action:
As supply chains become more localized and manufacturers demand greater flexibility, OpiFlex is here to help you stay ahead of the curve. Discover how our advanced robotic solutions can streamline your production lines, reduce downtime, and future-proof your operations. Contact us today to learn how we can help you build a more agile, resilient manufacturing environment.
Related articles
-
small series manufacturing fenceless safety Dynamic Program Generator Industrial robot applications Future of robotics in manufacturing
10 Years of Disruption: How OpiFlex Redefined Flexible Robotics in Manufacturing
Discover how OpiFlex transformed robot automation with ultra-flexibility and smart programming—10 years after winning the EU's top innovation award.
Read more -
Robotization Mobile Robot System flexible robotics high-flexibility production Fast programming for robots Industrial robot applications
How One Small Manufacturer Runs 4000 Products Per Year—24/7—with a Flexible Robot
Discover how a small wood industry manufacturer automates 4000 products/year per machine—24/7—with no robot skills required. Flexibility is the key.
Read more -
future-proof factories OpiFlex Dynamic Program Generator Industrial robot applications Flexible robotic applications Future of robotics in manufacturing
The Four Robotic Revolutions: How Flexibility Drives the Future of Manufacturing Automation
Discover the four robotic revolutions that have reshaped industrial automation. Explore how flexibility, from fixed robots to AI-driven cognitive machines, is transforming manufacturing.
Read more