Introducing Dynamic Flow Optimization: Revolutionizing Robot Programming for Small Series Manufacturing
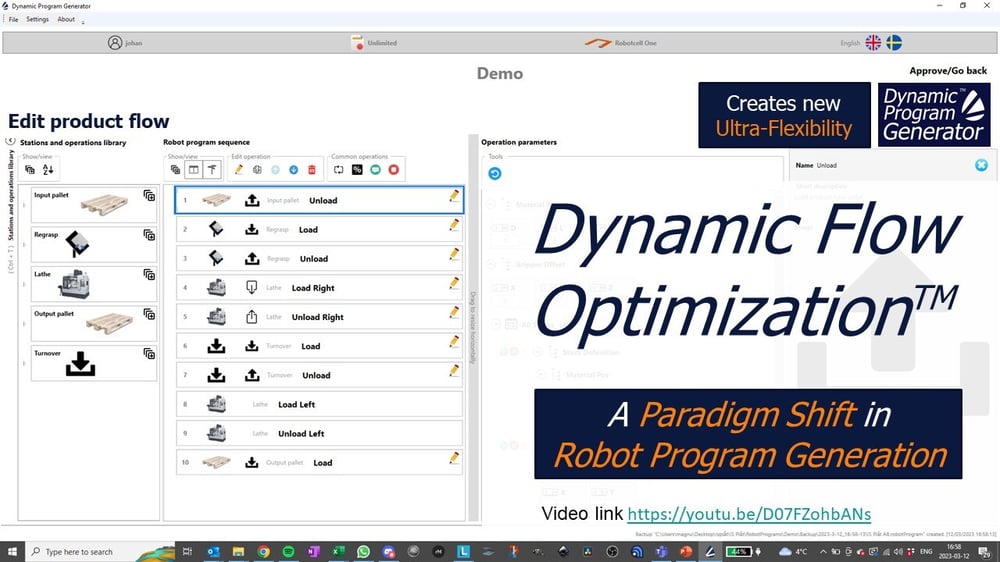
Introduction
In today's manufacturing landscape, the mega trend of high product mix and low volumes demands rapid and efficient robot programming solutions. Traditionally, creating robot programs is a time-consuming and complex task, often requiring specialists to spend around eight hours adding a new product to an existing program. While this is manageable for large series production, it becomes a significant bottleneck in small series manufacturing.
Enter Dynamic Flow Optimization, a groundbreaking feature in OpiFlex's patented Dynamic Program Generator, designed to make robot programming faster and simpler than ever before.
The Hassles of Traditional Robot Programming
Running small series manufacturing with high product mix and low volumes necessitates swift and straightforward robot programming to maintain profitability. However, traditional methods often fall short. Typically, it takes about eight hours for a specialist to incorporate a new product into an existing robot program. This duration is acceptable for large series production but impractical for small series and the increasingly popular high-mix, low-volume production environments.
Various solutions on the market aim to simplify robot programming. Yet, even the best of these still involve significant hassle, requiring consideration of logics, signaling, error handling, and more when adding a new product. With these solutions, the average programming time ranges from one to three hours for small changes, from start to finish.
OpiFlex's Dynamic Program Generator: A Revolutionary Solution
OpiFlex offers a world-unique, patented solution with its Dynamic Program Generator, eliminating the need for extensive programming skills. With this tool, users can create a completely new program in just one to five minutes, from start to finish, including configuring new input and output pallets. The Dynamic Program Generator simplifies the process by teaching the robot everything it needs to know about the cell and its movements, removing the need for users to handle paths, logics, signaling, and error handling.
Introducing Dynamic Flow Optimization
OpiFlex has now taken its innovative solution a step further with the introduction of Dynamic Flow Optimization. This add-on makes generating a robot program even faster and easier. With Dynamic Flow Optimization, you can add a completely different product with a totally new layout for the input and output pallets in just one to five minutes, without any programming skills.
Dynamic Flow Optimization allows users to focus solely on the flow of their products, as the robot optimizes sequences based on the tasks being performed by the machine or machines it tends. This feature dynamically adapts to the status of the machine or other stations within the robot cell, enabling the robot to run several products simultaneously across multiple machines, always optimizing for maximum efficiency and minimizing downtime.
Comparison with Other Easy Programming Solutions
Other easy programming solutions available on the market tend to be static and do not adapt to the status of the machine or other stations within the robot cell. The time required to add a new product to an existing robot program for a leading collaborative robot manufacturer tending a CNC machine can vary significantly:
-
Complexity of the Product:
- Simple Product: Minor adjustments could take a few minutes to a couple of hours.
- Complex Product: Major changes might take several hours to a full day.
-
Programming Experience:
- Experienced Programmer: Quicker completion.
- Novice Programmer: Longer duration, with more troubleshooting and testing.
-
Programming Environment:
- Polyscope (Native Programming Environment for Many Collaborative Robots): Generally user-friendly but can be time-consuming for complex changes.
- Offline Programming Software: Tools like RoboDK or similar can expedite the process.
-
Integration Requirements:
- Gripper Adjustments: Modifying grippers can add time.
- CNC Program Adjustments: Changes in the CNC machine's program can influence the timeline.
- Fixture Modifications: Adjustments to fixtures or jigs can add to the setup time.
-
Testing and Debugging: Thorough testing and debugging are essential and can take additional time.
Typical Timeline Estimates:
- Simple Changes: 1-3 hours.
- Moderate Changes: 4-8 hours.
- Complex Changes: 1-3 days.
Conclusion
Comparing OpiFlex's Dynamic Program Generator with other easy robot programming solutions highlights the unique advantages it offers. The introduction of Dynamic Flow Optimization further enhances these benefits, making it the fastest and simplest solution for small series manufacturing and high-mix, low-volume production environments. By dynamically handling multiple products and machines, OpiFlex ensures maximum efficiency and minimal downtime, setting a new standard in robot programming.
Related articles
-
small series manufacturing fenceless safety Dynamic Program Generator Industrial robot applications Future of robotics in manufacturing
10 Years of Disruption: How OpiFlex Redefined Flexible Robotics in Manufacturing
Discover how OpiFlex transformed robot automation with ultra-flexibility and smart programming—10 years after winning the EU's top innovation award.
Read more -
Robotization Mobile Robot System flexible robotics high-flexibility production Fast programming for robots Industrial robot applications
How One Small Manufacturer Runs 4000 Products Per Year—24/7—with a Flexible Robot
Discover how a small wood industry manufacturer automates 4000 products/year per machine—24/7—with no robot skills required. Flexibility is the key.
Read more -
future-proof factories industrial robotics high product mix, low volumes flexible robotics high-flexibility production adaptable manufacturing
Key Manufacturing Challenges and Trends in the U.S. for 2025
Discover the top U.S. manufacturing trends and challenges in 2025, from tariffs and AI to sustainability. Learn how companies can stay competitive.
Read more