The Future of Manufacturing: How Flexible Automation is Reshaping Industry
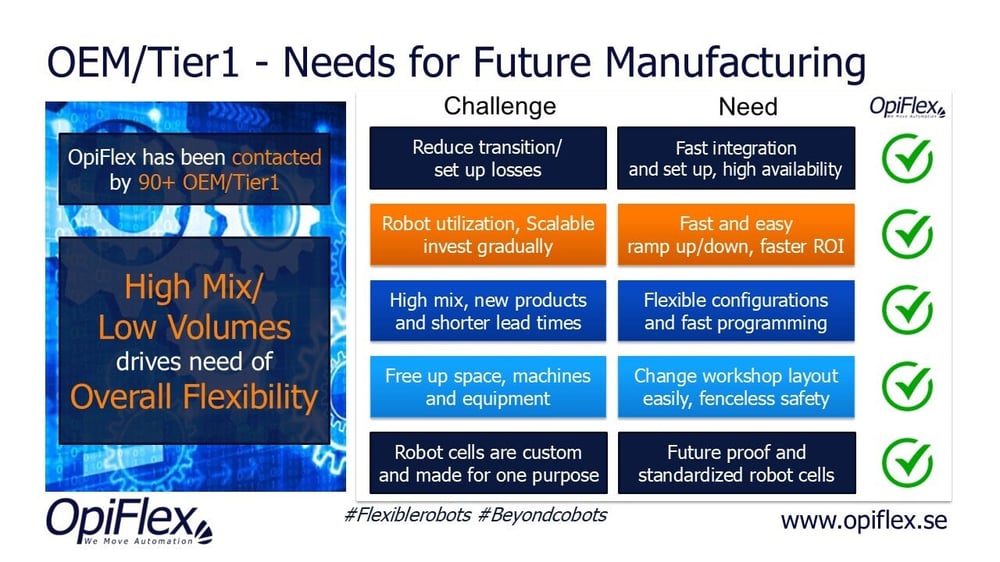
Introduction
The manufacturing industry is undergoing a dramatic transformation, driven by the shift toward high-mix, low-volume production, the increasing importance of sustainability, and the demand for greater flexibility in automation. Traditional fixed robotic systems struggle to keep up with these changing demands, leading manufacturers to seek future-proof, flexible robot solutions that enable rapid adaptation.
According to Nolan, A. (2021) in the OECD report Making Life Richer, Easier and Healthier: Robots, Their Future and the Roles for Public Policy, manufacturers across industries have five critical needs:
- Rapid robot integration and installation, reducing deployment time from weeks to days.
- Fast production scale-up and scale-down, allowing for agile response to market demands.
- Flexible robot configurations and programming, enabling quick product changes and mix adjustments.
- Easily modified layouts without fences, ensuring adaptability in dynamic production environments.
- Standardized, future-proof solutions, allowing robots to be repurposed as needs evolve.
At OpiFlex, we see these challenges firsthand when working with manufacturers who need automation to be adaptable, cost-effective, and easy to implement without disrupting production. Our approach focuses on providing flexible, mobile robot solutions that meet these needs in a reliable and scalable way.
1. The Shift to High-Mix, Low-Volume Production
1.1 A New Manufacturing Paradigm
The manufacturing landscape is shifting away from traditional high-volume, low-mix production toward high-mix, low-volume (HMLV) manufacturing. Customers now demand greater product variety, shorter production cycles, and mass customization, which challenges conventional automation systems.
Unlike traditional robotic setups optimized for long, repetitive production runs, HMLV environments require frequent reprogramming and retooling, leading to downtime and inefficiencies. Many manufacturers still rely on fixed robot systems with safety fences, which limit adaptability and hinder rapid changes in production layouts.
To stay competitive, manufacturers need flexible automation that:
- Allows for rapid reprogramming without requiring extensive expertise.
- Enables easy relocation of robots to different workstations.
- Supports multiple product variants on the same production line.
1.2 OpiFlex’s Role in Flexible Robotics
Companies like OpiFlex address these challenges by offering mobile and flexible robotic solutions. Unlike traditional static industrial robots, OpiFlex robots can be easily moved between workstations and reprogrammed in minutes—up to 50 times faster than conventional methods.
As Nolan (2021) highlights, reducing integration time is crucial for ensuring production agility. OpiFlex enables this by combining fast programming, mobile docking, and fenceless safety, allowing manufacturers to automate efficiently without being locked into fixed layouts.
2. Sustainability as a Core Priority in Manufacturing
2.1 Meeting Regulatory and Market Demands
Sustainability has become a major driver of change in manufacturing. Governments and regulatory bodies, such as the European Union's Corporate Sustainability Reporting Directive (CSRD), are pushing companies to adopt eco-friendly production practices.
Manufacturers must now consider:
- Energy-efficient automation to reduce operational costs and environmental impact.
- Minimizing material waste through precision-controlled robotics.
- Local production strategies to cut down on global transportation emissions.
2.2 How OpiFlex Contributes to Sustainable Automation
The OECD report (Nolan, 2021) emphasizes that flexible, mobile robotic solutions can significantly improve resource efficiency by enabling multi-use deployments across different production areas.
OpiFlex’s mobile, fenceless robot solutions help manufacturers reduce energy consumption and material waste by:
- Minimizing downtime and improving machine utilization, reducing overall power consumption.
- Reducing overproduction and scrap by enabling agile, on-demand manufacturing.
- Supporting localized production, reducing logistics-related emissions.
By integrating scalable and adaptable automation, manufacturers can meet both economic and environmental goals without major reinvestments in infrastructure.
3. Key Automation Trends Shaping the Future
3.1 The Rise of Scalable, Flexible Automation
According to the International Federation of Robotics (IFR), manufacturers are prioritizing scalable, flexible automation to keep up with fluctuating demand. Nolan (2021) further highlights that many large manufacturers find themselves locked into fixed robot units, making it difficult to adapt to new products or factory layouts.
OpiFlex provides a future-proof approach by offering robots that:
- Deploy in days instead of weeks, cutting integration time significantly.
- Reconfigure production layouts without costly modifications.
- Support diverse product lines with minimal reprogramming effort.
3.2 Overcoming Traditional Robot Limitations
Fixed robotic systems often require weeks of programming and integration, leading to high costs and long downtime. In contrast, OpiFlex’s next-generation mobile robots feature:
- Intuitive, fast programming interfaces, eliminating the need for expert coders.
- Seamless docking systems, enabling robots to switch between tasks effortlessly.
- Patented fenceless safety solutions, ensuring high-speed operation without physical barriers.
This approach not only reduces costs but also ensures manufacturers can adapt their automation strategy to evolving production needs.
4. How Manufacturers Can Stay Ahead with Flexible Robotics
4.1 A Trustworthy Path to Flexible Automation
The benefits of flexible robotic solutions extend beyond operational efficiency. Companies that invest in adaptable automation experience:
✔ Lower integration costs – Quick deployment reduces installation expenses.
✔ Increased uptime – Faster reprogramming minimizes production interruptions.
✔ Better scalability – Robots can be easily repurposed for new tasks.
✔ Higher competitiveness – Ability to meet diverse customer demands efficiently.
At OpiFlex, we take a structured and reliable approach to automation, ensuring that our solutions fit seamlessly into existing workflows without unnecessary complexity. Our patented technologies ensure that even large industrial robots can be flexible and safe without compromising performance.
4.2 Taking the Next Steps
For manufacturers looking to stay ahead, the key is to embrace automation solutions that are:
- Flexible: Robots should adapt to changing production needs.
- Fast to deploy: Installation should take days, not weeks.
- Future-proof: Standardized solutions ensure long-term usability.
Conclusion: The Future of Manufacturing is Flexible
As the OECD report (Nolan, 2021) underscores, the future of automation lies in flexibility, adaptability, and rapid integration. Manufacturers that continue to rely on rigid, fenced robotic systems will struggle to compete in an era of high-mix, low-volume production and sustainability-driven decision-making.
By investing in mobile, easy-to-program, and future-proof robotics, manufacturers can reduce costs, increase efficiency, and remain competitive in a rapidly evolving market. OpiFlex provides a proven, industry-leading approach to flexible automation, ensuring that manufacturers stay ahead of change with confidence.
🔹 Want to explore a smarter way to automate?
Contact OpiFlex today to learn how our flexible robot solutions can support your production needs.
Related articles
-
small series manufacturing fenceless safety Dynamic Program Generator Industrial robot applications Future of robotics in manufacturing
10 Years of Disruption: How OpiFlex Redefined Flexible Robotics in Manufacturing
Discover how OpiFlex transformed robot automation with ultra-flexibility and smart programming—10 years after winning the EU's top innovation award.
Read more -
Robotization Mobile Robot System flexible robotics high-flexibility production Fast programming for robots Industrial robot applications
How One Small Manufacturer Runs 4000 Products Per Year—24/7—with a Flexible Robot
Discover how a small wood industry manufacturer automates 4000 products/year per machine—24/7—with no robot skills required. Flexibility is the key.
Read more -
future-proof factories industrial robotics high product mix, low volumes flexible robotics high-flexibility production adaptable manufacturing
Key Manufacturing Challenges and Trends in the U.S. for 2025
Discover the top U.S. manufacturing trends and challenges in 2025, from tariffs and AI to sustainability. Learn how companies can stay competitive.
Read more